Plant of tomorrow
Schulte - Elektrotechnik’s new production and warehousing facility will allow it to take a further step towards becoming an energy self-sufficient company.
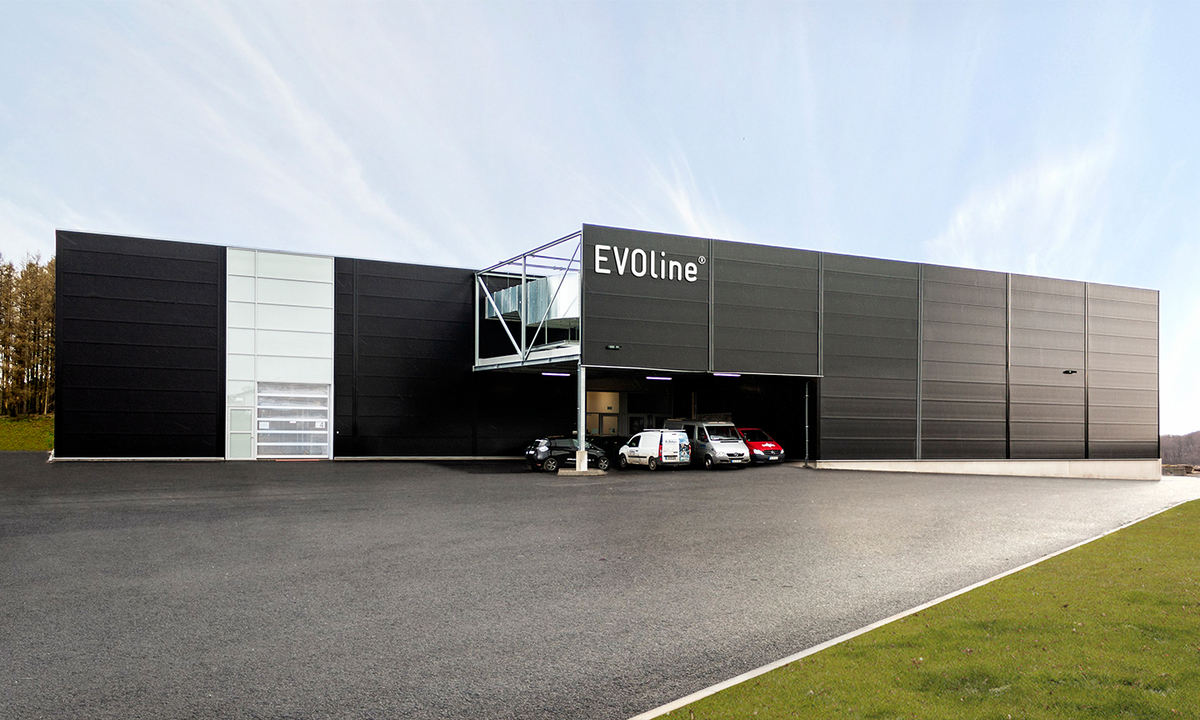
Sustainability and environmental protection have long since been some of industry’s key issues and have always been close to Schulte - Elektrotechnik’s heart. In terms of sustainability, the company has consistently set a good example.
What started with the construction of the company’s headquarters in 1973 and continued with an extension in 2014, is now being taken to a new level at the Rosmart business park in Lüdenscheid. This is where Schulte - Elektrotechnik is adding to its facilities by building a new production shed and warehouse for tool making, injection moulding of plastics and processing semi-finished products. The new build reaches thresholds much lower by 60% than those specified by the German Energy Saving Ordinance (EnEV) and therefore plays a key role in cutting the carbon footprint. The project is a prime example of energy-efficient construction and therefore attracted a subsidy of €250,000. But Schulte - Elektrotechnik’s objectives are even more ambitious because its new goal is to save even more or generate energy itself in future.
The new building isn’t just a shot in the arm to Schulte - Elektrotechnik’s sustainable concept but is an indication that it sees plenty of long-term potential at the Lüdenscheid site. The new plant is situated on land 22,000 m² in size, with floorspace for production of 4,200 m². It is divided into two halves, one of which accommodates plastic production, tool making and the Bihler stamping and forming machines and the other the material and parts warehouse and incoming goods. Vast amounts of energy are required to get the machines running and supply the factory with enough electricity. Therefore, constructing an energy self-sufficient building was an exciting challenge for the planners. But it was worth it in the end. The company required energy for the electricity supply, cooling equipment and underfloor heating, which was fitted by means of thermally activated floor panels to the whole production and warehouse facility. And energy was gained from the production processes and a photovoltaic system on the roof. As a result, there is virtually zero need to draw on external energy supplies to keep the building fully functional.
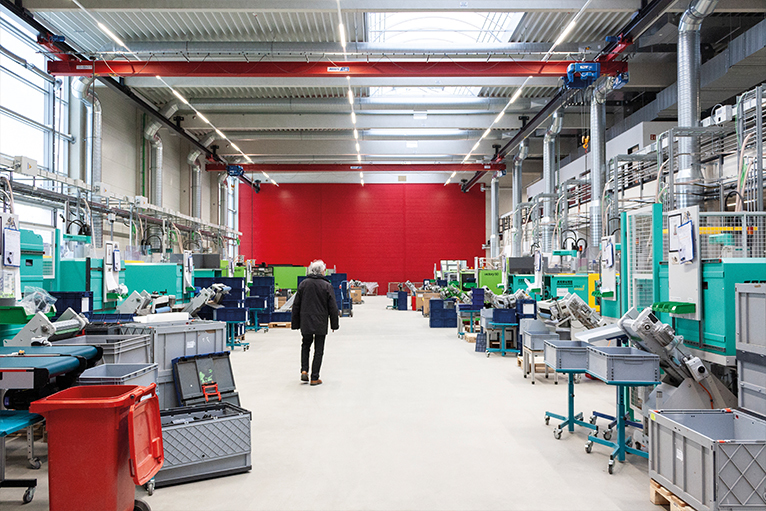
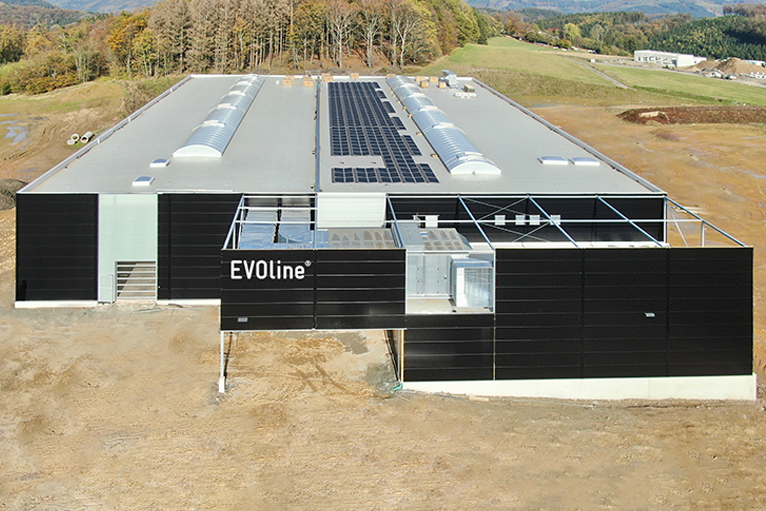
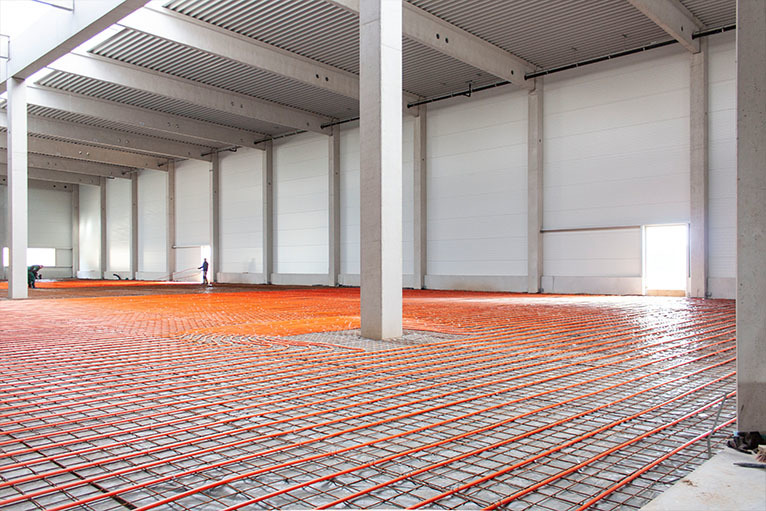
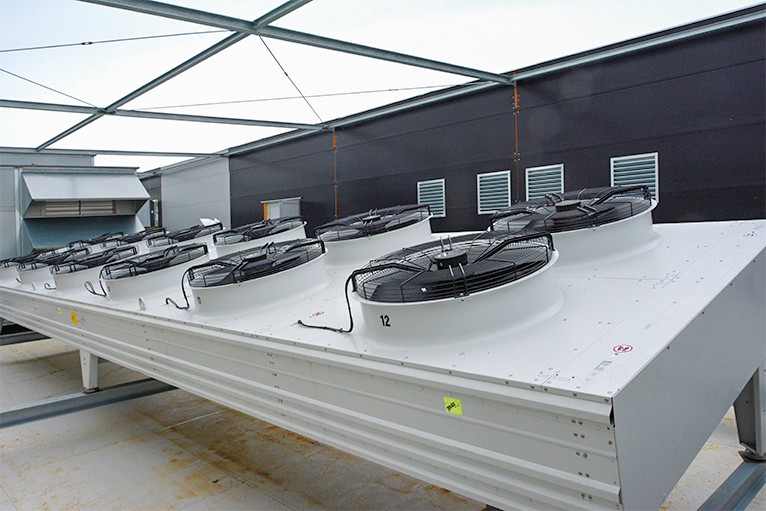
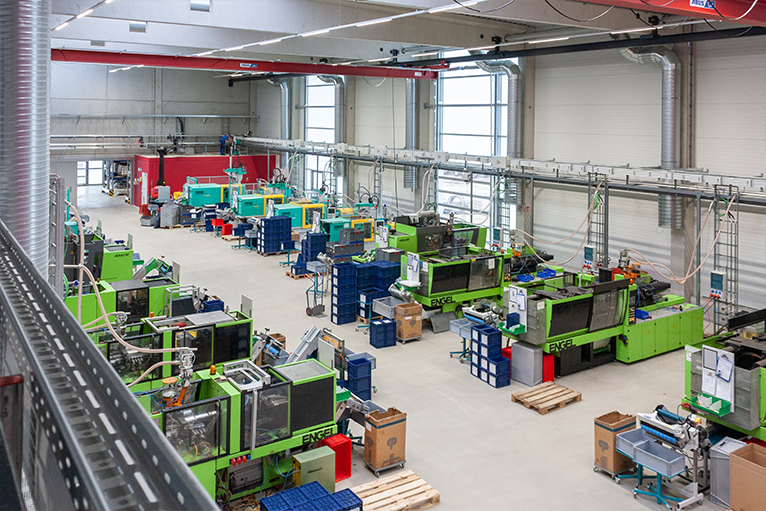
The company is just as innovative and energy efficient today as it was in the past. In terms of building technology, even in 1973 Schulte - Elektrotechnik’s headquarters were already ahead of their time. For example, the first building already had carbon neutral heating because the waste heat from the plastic injection moulding department was used for the underfloor heating. This advanced concept was expanded when the company was extended in 2014. During the rebuilding phase, Schulte - Elektrotechnik fitted new ceiling and underfloor heating. The vast system of pipes ensures consistent temperature in the offices and, in the process, only consumes geothermal energy from ten, 100-metre-deep drill holes in the process. Geothermal energy is thermal energy generated and stored in the earth and it is used to generate hot water for heating in the winter. If necessary, a heat pump is used to pump the desired temperature into the heating circuits. In summer, excess heat is transferred from the building via the water circuits to the ground.